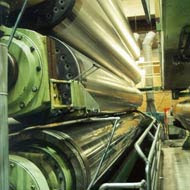
Roll Alignment, specifically, is the alignment and measurement of roll parallelism in plant machinery that is typically used to feed sheet materials. Typical industrial applications include:
- Paper and Pulp manufacture
- Printing Works
- Textile Mills
- All types of Sheet Manufacturing
Problems associated with the misalignment of Rolls include:
- Drift and tracking of sheet materials during feed
- Wrinkling and Breakages in paper / material
- Uneven gloss rate in paper manufacture
- High scrap rates of materials
Roll alignment is conducted using sophisticated Laser Alignment Systems, such as the ROLL200 laser alignment system produced by Fixturlaser. Fixturlaser systems are widely regarded throughout industry as the most professional, high precision, user-centred systems available.
Industrial Applications for Roll Alignment
The Headbox:
- Measurement of straightness of the headbox lip profile
- Measurement of parallelism between the headbox and breast roll
The Foil Section:
- Measurement of the flatness of the foils
The Press Section:
- Measurement of the horizontal parallel alignment of the press rolls
- Straightness measurement of the press rolls
- Check of the deflection-compensating rolls
The Dryer Section:
- Measurement of horizontal parallel alignment of the rolls
The Calendar:
- Measurement of horizontal parallel alignment of the rolls
The Winder:
- Horizontal parallel alignment of the Tambour rolls
The Coating Section:
- Horizontal parallel alignment of the rolls
Roll Alignment Systems
The Fixturlaser Roll200 is an innovative laser alignment system providing advanced measurement capabilities for paper machines and other roll applications. The system is easy to use for measurement and alignment as well as for documenting the results.
The Fixturlaser Roll200 is built on the same platform used as basis for other Fixturlaser alignment systems. The Fixturlaser Platform offers the advantage of upgradeability to other Fixturlaser products, to provide capabilities for:
Vertical Shaft Roll Alignment
- Horizontal Shaft Alignment
- Softfoot Measurement
- Straightness Measurement
- Cardan Shaft Alignment
- Levelling Measurement
- Flatness Measurement
Fixturlaser Roll Alignment System Benefits
The Fixturlaser Roll200 features:
- Easy to use and easy to learn. The intuitive user interface guarantees high usability.
- High accuracy - one micron resolution (1/1000mm)
- Quick, easy and flexible setup provides access to alignment wherever and whenever you need it
- Live values on-screen provide constant feedback on roll position as adjustments are made
- Flexibility allows use of either floor datum or a selected roll as the reference point for measurements
- Onboard system memory, plus printer and data ports allow complete documentation of every roll measurement
Technical specification of the Roll 200 System:
- Measuring distance: Up to 50 meters (150 ft)
- Displayed measurement result resolution: 0,001 mm (0,1 mils)
- Operating temperature range: 0-40°C (32 - 122°F)
- Power supply: Standard batteries
- Operating time: Depending on operation cycle 10 - 20 hrs
- Weight complete system: 32 kg
Roll Alignment Applications Commonly Found Throughout the Paper Industry
The parallelism of the rolls, both vertically and horizontally, may affect the drift and wear of the felt, the drying capacity of the paper and may cause breakages in the paper. Especially parallelism in the press nip is important or the pressure will be uneven causing problems with the de-watering process.
Benefits:
- Less scrap due to uniform fibre structure
- More output due to the possibility to increase production speed
- Increased time between replacement of wire gives less downtime
- Less energy consumption due to efficient de-watering
Measurements:
- Horizontal and vertical parallelity of rolls
- Roll parallelism has a direct impact on the paper transportation
- Compensation is made by adjustable rolls, but severe misalignment can result in wrinkles and breakages at the edges
Roll Alignment - Dryer Section
In this section, the problems are similar to the press sections, although we would like to point out the problem with wrinkles and breakages in the paper sheets. The amount of rolls in the web path is large in the dryer section and increases the importance of roll parallelism.
Benefits:
- Increased uptime
- Increased time between felt changes
- Reduced scrap production
- Increased product quality
- Possibility to increase production speed
Measurements:
- Horizontal and vertical parallelism of rolls
- Straightness of doctor blades
Roll Alignment - Forming Table
In this section, parallelism between the breast roll and the drive rolls is important, or the drift and wear of the wire will be affected. The surface of the paper sheet is affected if the dandy roll is not parallel to the forming table. The pick up roll and the couch roll may cause breakages and wrinkles if they are not kept parallel, and the suction process may be affected. The levelling of the forming table is another important factor in this section, that will especially affect the de-watering pro-cess and the deterioration of the foils.
Benefits:
- Efficient de-watering process and uniform fibre structure will improve the paper quality
- Increased de-watering capability gives possibility to
- Increase production speed
- Increased lifetime of the wire
- Reduced energy consumption for the vacuum pumps
Measurements:
- Flatness measurement and levelling of the forming table
- Parallelism of drive rolls
- Parallelism of forming rolls
Roll Alignment - Head Box
It is important that the breast roll is parallel to the apron board. If the air gap differs, it will cause problems with the consistency of the paper. It is also important that the apron board is straight and the slice gap is correct in order to get a uniform output of paper pulp on to the forming table.
Benefits:
- Uniform paper structure and thickness
- Reduced rate of scrap paper
- Increased efficiency in the dewatering process and possibility to increase production speed
- Reduced risk of breaking the slice tip
Measurements:
- Straightness measurement on apron board
- Parallelism between apron board lip and breast roll
Roll Alignment - Finishing Calendars
The parallelism is important in the calendar, both vertically and horizontally, or the roll nip will differ over the roll length. In some calendars, there is a nip offset that has to be considered.
Benefits:
- Uniform gloss
- Reduced scrap production
- Increased time between roll replacement
- Possibility to increase production speed
Measurements:
- Horizontal and vertical parallelism of rolls
- Set calendar nip offset
Roll Alignment - Winders
Poor parallelism between the calendar rolls, the reel drum and spool may create problems with a high rate of scrap paper as a result. Also the paper may drift sideways during the reeling, creating problems with wrinkles and difficulties when cutting the paper.
Benefits:
- Less scrap paper
- Increased production capacity
Measurements:
- Horizontal and vertical roll parallelism