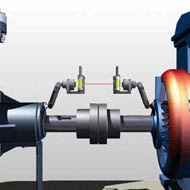
Machines operating in perfect alignment run at their most efficient. Misaligned shafts are recognised as one of the greatest contributors to plant breakdowns, due to the increased forces placed on bearing, mechanical seals, internal components and motor drives.
A modern Laser Shaft Alignment system utilises laser-based technology to ensure that the shafts are coupled together along a perfect rotational centreline.
A Laser Shaft Alignment System offers precision alignment of shafts to within hundredths of a millimetre. The latest Shaft Alignment System manufactured by Fixturlaser offers sophisticated laser alignment technology that is fast and easy to operate in the field.
Industrial Applications for Laser Shaft Alignment
Laser Shaft Alignment offers benefits in any industry where rotating equipment applications are used:
- Direct drive Fans
- Motor-driven Pumps
- Gearboxes
- Compressors
- Turbines
- Transfer boxes
- Propeller shafts
- Couplings
- Conveyors
- Generators
- Mixers
Common Industries that utilise Laser Shaft Alignment as part of their Maintenance regime include:
- Manufacturing and processing industries
- Wind turbines
- Marine Craft and Shipbuilding
- Paper and Pulp Industries
- Water and Waste Water Pumping
- Construction Industry
- Gas & Oil Industries
- Chemical & Pharmaceutical Industries
- General industry
Easy to use for Express Alignment in the field
The Fixturlaser XA system is characterised by its easy-to-use interface – equally beneficial for alignment professionals using the equipment on a regular basis, and for maintenance technicians conducting periodic alignment checks.
The XA system features a colour LCD touchscreen, with on-screen icons and animated display which guides users through the alignment process.
The XA system utilises CCD digital laser technology, which does not suffer from interference problems in the field, such as bright sunlight, which affect the traditional optical laser systems used by other manufacturer's systems.
Additionally, the XA utilises a line laser (instead of a dot-laser) and a 30mm laser detector in each laser receiver, practically eliminating the need to conduct rough alignment checks.
Pre-assembled fixtures enable the lasers to be attached to the application in seconds, and Bluetooth connectivity eliminates the need for cables from the laser units to the display unit.
The XA system features an Express Alignment mode which automatically samples alignment data once the system is set-up. The net result - Alignment measurements can be quickly and easily conducted in the field in under 5 minutes from opening the lid of the case!
Technologically sophisticated for Precision Alignment
- Bluetooth (Class 2) connectivity between display unit and laser transmitters
- Measurement range up to 10 metres
- 20 hours typical use from rechargeable Li-Ion batteries
- Slim laser units: 79mm x 77mm x 33mm
- 128Mb Flash Storage Memory
- IP65 rated Environmental Protection
- Standard package includes:
- Horizontal Shaft Alignment
- Vertical Shaft Alignment
- Softfoot Check
- Target Values
Expansion packages include:
- Spacer Shaft Alignment software package
- Machine Train Alignment software package
- Offset Shaft Alignment software & fixtures package
- OL2R (offline to running) software and fixtures package for measuring dynamic movements.